Chemical engineering is a discipline that combines principles of chemistry, physics, biology, and mathematics to design and operate processes for producing, transforming, and transporting materials. In this complex field, efficiency and accuracy are critical, and this is where simulation tools come into play. These tools are essential in modeling chemical processes, allowing engineers to predict and optimize system behavior before implementing changes in real-world applications.
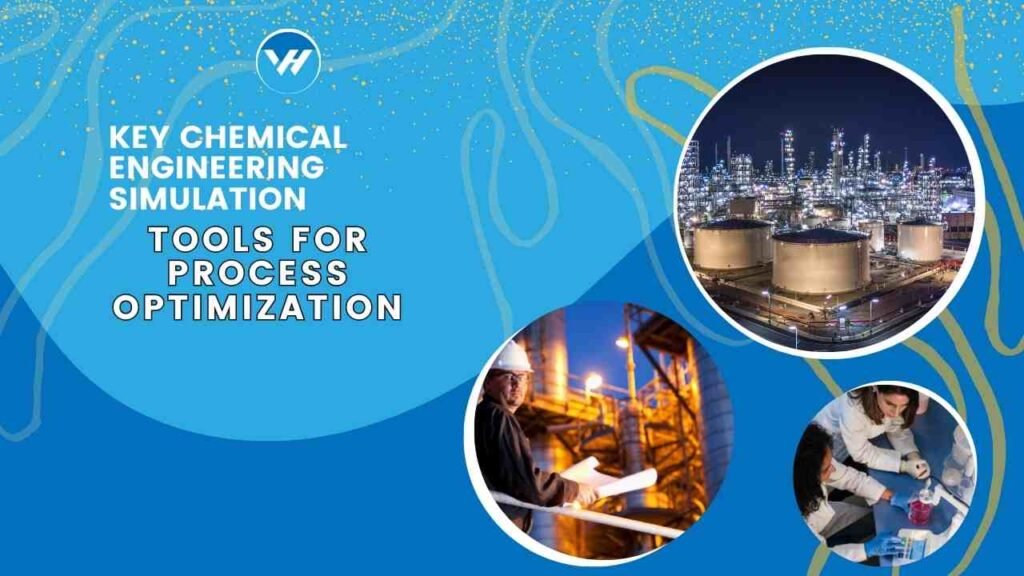
Table of Contents
ToggleImportance of Process Optimization in Chemical Engineering
Process optimization is vital in chemical engineering as it ensures that processes are running at their most efficient and cost-effective levels. This not only maximizes production but also minimizes waste and energy consumption. In an industry where small inefficiencies can lead to significant costs, optimization is not just a best practice—it’s a necessity.
The Role of Simulation Tools in Process Optimization
Simulation tools have revolutionized the way chemical engineers approach process optimization. These tools enable engineers to create detailed models of processes, run various scenarios, and identify the best operating conditions. By simulating different process configurations, engineers can make informed decisions that lead to improved performance, safety, and profitability.
Understanding Process Optimization
What is Process Optimization?
Process optimization refers to the practice of adjusting a process to make it as effective, efficient, and cost-effective as possible. In chemical engineering, this often involves tweaking variables such as temperature, pressure, and flow rates to achieve the desired output with minimal input.
Benefits of Process Optimization in Chemical Engineering
Optimizing processes offers numerous benefits, including reduced operational costs, increased production rates, improved product quality, and enhanced safety. It also plays a crucial role in sustainability efforts by minimizing resource consumption and reducing environmental impact.
Challenges in Achieving Process Optimization
While process optimization is highly beneficial, it comes with challenges. These include the complexity of chemical processes, the need for precise data, and the potential for unforeseen interactions between variables. Additionally, the initial costs of optimization tools and the time required to learn and implement them can be barriers for some companies.
Overview of Chemical Engineering Simulation Tools
What are Chemical Engineering Simulation Tools?
Chemical engineering simulation tools are software applications designed to model chemical processes. They allow engineers to create virtual representations of systems, run simulations under different conditions, and analyze the outcomes. These tools are indispensable in modern chemical engineering for both design and operational purposes.
The Evolution of Simulation Tools in the Chemical Industry
The development of simulation tools has been driven by advances in computing power and software engineering. Early tools were limited in scope and capability, but today’s simulations can model entire plants with a high degree of accuracy. This evolution has made simulation tools more accessible and versatile, allowing engineers to tackle more complex challenges than ever before.
Key Chemical Engineering Simulation Tools
Aspen Plus
Features and Capabilities
Aspen Plus is one of the most widely used simulation tools in chemical engineering. It offers a comprehensive set of features for process modeling, including rigorous thermodynamic models, extensive chemical component databases, and advanced process optimization algorithms. Aspen Plus is known for its ability to handle both steady-state and dynamic simulations, making it a versatile tool for various applications.
Applications in Process Optimization
Aspen Plus is particularly useful in optimizing energy use, improving yield, and reducing emissions. Its ability to simulate complex chemical reactions and mass transfer processes makes it a powerful tool for engineers looking to enhance process efficiency. For instance, in energy-intensive industries, Aspen Plus can be used to identify opportunities for heat integration, leading to significant cost savings.
HYSYS
Features and Capabilities
HYSYS, developed by AspenTech, is another prominent simulation tool in the chemical engineering sector. It is renowned for its user-friendly interface and powerful simulation capabilities. HYSYS excels in modeling oil and gas processes, making it a go-to tool for engineers in the petrochemical industry.
Applications in Process Optimization
HYSYS is often used for optimizing separation processes, such as distillation, which are critical in the chemical and petrochemical industries. By simulating various configurations, engineers can determine the optimal design and operating conditions for these processes, leading to improved efficiency and lower operating costs.
CHEMCAD
Features and Capabilities
CHEMCAD is a flexible and customizable simulation tool that caters to a wide range of chemical processes. It offers a robust suite of modules that can be tailored to specific applications, from basic chemical processing to complex multi-unit operations. CHEMCAD is known for its intuitive interface and comprehensive reporting features.
Applications in Process Optimization
CHEMCAD is particularly useful for optimizing batch processes, which are common in industries such as pharmaceuticals and specialty chemicals. Engineers can use CHEMCAD to simulate different batch sequences and identify the most efficient production strategy. This can lead to reduced cycle times and improved product consistency.
PRO/II
Features and Capabilities
PRO/II, developed by AVEVA, is a steady-state process simulator that is widely used in the design and optimization of chemical processes. It features a range of thermodynamic models and unit operation modules that allow engineers to simulate and optimize various processes. PRO/II is especially valued for its accuracy and reliability in process design.
Applications in Process Optimization
PRO/II is commonly used in the design of new processes and the optimization of existing ones. It is particularly effective in optimizing distillation processes, where it can be used to model and refine column configurations to achieve the best separation performance with minimal energy consumption.
gPROMS
Features and Capabilities
gPROMS is a sophisticated process modeling tool that is known for its advanced capabilities in dynamic simulation and optimization. It is particularly well-suited for processes that involve complex kinetics, such as polymerization and biochemical reactions. gPROMS offers a high level of customization, allowing engineers to develop detailed models tailored to specific processes.
Applications in Process Optimization
gPROMS is often used in the fine-tuning of complex chemical processes, where it can model dynamic behavior and optimize process conditions over time. This makes it an ideal tool for processes that are sensitive to changes in operating conditions, such as reaction kinetics or phase transitions.
Selecting the Right Simulation Tool
Factors to Consider When Choosing a Simulation Tool
When selecting a simulation tool, engineers must consider several factors, including the complexity of the process, the specific features required, the ease of use, and the cost of the software. It’s also important to consider the level of support and training available for the tool, as well as its compatibility with existing systems.
Comparing the Key Simulation Tools
Each simulation tool has its strengths and weaknesses, so the choice often depends on the specific needs of the project. For example, Aspen Plus might be the best choice for a chemical plant looking to optimize energy use, while HYSYS could be more suitable for a petrochemical facility focused on refining operations. Comparing tools based on their features, cost, and user feedback can help engineers make an informed decision.
The Future of Simulation Tools in Chemical Engineering
Emerging Trends in Simulation Technology
The field of simulation technology is constantly evolving, with new trends such as cloud computing, real-time simulation, and digital twins gaining traction. These advancements are making simulation tools more powerful, accessible, and integrated into the broader digital landscape of the industry.
The Impact of AI and Machine Learning on Simulation Tools
Artificial Intelligence (AI) and Machine Learning (ML) are beginning to play a significant role in enhancing simulation tools. By incorporating AI and ML algorithms, simulation tools can improve predictive accuracy, automate optimization processes, and provide deeper insights into complex systems. This integration is expected to drive significant improvements in process optimization capabilities.
How to Get Started with Simulation Tools
Steps to Implement Simulation in Process Optimization
- Identify Process Challenges: Start by pinpointing the specific challenges or inefficiencies in your process that need to be addressed. This could be anything from energy waste to low yield or excessive production time.
- Choose the Right Simulation Tool: Based on the nature of the process and the specific optimization goals, select a simulation tool that offers the necessary features and capabilities.
- Gather Process Data: Collect all relevant data, including process variables, material properties, and operating conditions. Accurate data is crucial for building a reliable simulation model.
- Build the Simulation Model: Use the chosen tool to create a detailed model of the process. This may involve defining unit operations, setting up flow diagrams, and inputting process parameters.
- Run Simulations: Conduct simulations under various scenarios to explore different process configurations. This helps identify the optimal conditions for the desired outcomes.
- Analyze Results: Carefully analyze the simulation results to determine the best course of action. Look for opportunities to improve efficiency, reduce costs, or enhance safety.
- Implement Changes: Once the optimal process conditions have been identified, implement these changes in the actual process. Monitor the process closely to ensure that the expected improvements are realized.
- Continuous Improvement: Process optimization is an ongoing effort. Continue to use simulation tools to explore new opportunities for improvement as process conditions or business goals change.
Resources for Learning and Training
- Online Courses: Platforms like Coursera, edX, and Udemy offer courses on chemical engineering simulation tools, covering both basics and advanced topics.
- Webinars and Workshops: Many simulation software providers offer webinars and workshops to help users get the most out of their tools.
- User Manuals and Documentation: Comprehensive user guides and documentation are available from software vendors to help engineers navigate the features of the tools.
- Professional Organizations: Organizations such as AIChE (American Institute of Chemical Engineers) often provide resources, including training sessions and conferences focused on simulation tools.
Conclusion
Simulation tools have become indispensable in chemical engineering, offering a powerful means to optimize processes, reduce costs, and improve efficiency. Tools like Aspen Plus, HYSYS, CHEMCAD, PRO/II, and gPROMS each offer unique features tailored to different aspects of chemical engineering, from energy optimization to dynamic process modeling.
The selection of the right simulation tool depends on the specific needs of the process and the desired outcomes. By integrating these tools into process optimization efforts, chemical engineers can achieve significant improvements in performance, sustainability, and profitability.
In today’s competitive and fast-evolving chemical industry, the ability to simulate and optimize processes is more important than ever. Simulation tools not only help engineers design better processes but also enable them to respond quickly to changing market demands and technological advancements. As these tools continue to evolve, they will play an increasingly critical role in the future of chemical engineering.
FAQs
1. What is the best simulation tool for process optimization?
The best simulation tool for process optimization depends on the specific needs of the process and the industry. Aspen Plus is widely regarded for its versatility in various chemical processes, while HYSYS is preferred for petrochemical applications. For batch processes, CHEMCAD is often the tool of choice.
2. How do simulation tools benefit chemical engineers?
Simulation tools allow chemical engineers to model processes accurately, explore different scenarios, and optimize operating conditions. This leads to improved efficiency, cost savings, and enhanced safety in chemical processes.
3. Can small companies afford these simulation tools?
While some simulation tools can be expensive, many vendors offer scaled-down versions or cloud-based subscriptions that are more affordable for small companies. Additionally, the cost of these tools can often be justified by the savings and efficiency improvements they enable.
4. How difficult is it to learn to use simulation tools?
Learning to use simulation tools can be challenging, especially for complex processes. However, many resources are available, including online courses, user manuals, and vendor training sessions, to help engineers gain proficiency in using these tools.
5. What is the future of simulation tools in chemical engineering?
The future of simulation tools in chemical engineering is likely to be shaped by advances in artificial intelligence, machine learning, and real-time simulation. These technologies will enable more accurate predictions, automated optimizations, and seamless integration with digital twins and other Industry 4.0 innovations.